Magnetic polishing machine replaces special stainless steel polishing machine
Under the background of transformation and upgrading of manufacturing industry, traditional stainless steel polishing technology is facing multiple challenges of efficiency, environmental protection and precision processing. As a non-contact polishing technology, magnetic polishing machine has gradually become an innovative solution to replace traditional stainless steel special polishing machine with its unique advantages. This technology not only reshapes the underlying logic of polishing process, but also drives the metal surface treatment industry to move towards high efficiency, precision and green.
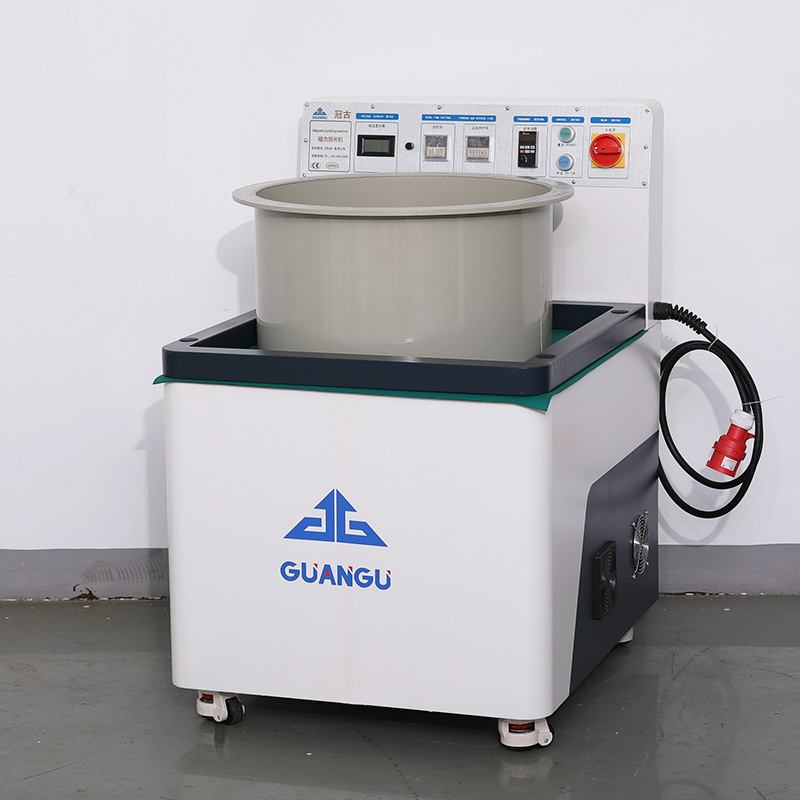
- Technological breakthrough: from mechanical friction to magnetic field drive
Traditional stainless steel polishing machine relies on the mechanical friction between grinding wheel, abrasive and workpiece to remove surface burrs, and there are three major pain points: first, the heat energy generated by high-speed rotation can easily cause workpiece deformation; second, there are polishing dead angles in complex structural parts; third, the abrasive loss is fast and the maintenance cost is high. The magnetic polishing machine drives the stainless steel needle abrasive through a high-frequency alternating magnetic field to form a high-speed eddy current motion, realizing 360° dead angle-free polishing. Taking a hardware company in Zhejiang as an example, after the special-shaped stainless steel fasteners it produces are polished by magnetic polishing, the yield rate is increased from 82% to 98%, and the processing time of a single piece is shortened by 40%. This non-contact energy transmission method completely avoids the risk of physical damage in traditional processes.
- Efficiency Leap: Reconstruction of the Cost of the Whole Process
From the perspective of the cost analysis of the whole life cycle, the magnetic polishing machine shows significant advantages. Comparative data from a medical device factory in Dongguan shows that the traditional polishing machine consumes 58 degrees of electricity per day, while the magnetic equipment only consumes 21 degrees, with an energy saving rate of 63.8%; the abrasive replacement cycle is extended from 7 days to 90 days, and the cost of consumables is reduced by 75%. More importantly, the equipment can achieve fully automatic continuous operation, reducing manual intervention by 80%, which is of strategic value to the manufacturing industry where labor costs continue to rise. According to industry estimates, after enterprises adopt magnetic polishing technology, the comprehensive production cost can be reduced by 30%-45%.
- Green Smart Manufacturing: Dual Evolution of Environmental Protection and Precision
Stricter environmental protection policies force industrial reform. There is no dust pollution during magnetic polishing, and wastewater discharge is reduced by 90%, which fully complies with the EU RoHS standard. A certain auto parts company in Qingdao reduces the cost of hazardous waste treatment by more than 1.2 million yuan each year through equipment upgrades. In terms of machining accuracy, magnetic polishing can achieve a mirror effect of Ra0.05μm and maintain a dimensional tolerance of ±0.01mm for workpieces, which is irreplaceable in high-end manufacturing fields such as precision medical devices and semiconductor accessories. Japan’s FANUC has integrated it into the intelligent production line to achieve unmanned precision polishing.
IV. Application boundaries and future prospects
At present, magnetic polishing machines are still limited in the field of ultra-large workpiece processing, but derivative technologies such as nano magnetorheological polishing are breaking through size limitations. With the outbreak of demand for micro-precision parts in 5G communications, aerospace and other fields, it is estimated that the global magnetic polishing market size will exceed US$3.2 billion in 2025, with an annual compound growth rate of 18.7%. For manufacturing companies, seizing the window period of technology iteration and taking the lead in completing the polishing process upgrade will take the lead in the competition for quality improvement, efficiency increase and sustainable development.
This technological revolution triggered by magnetic polishing not only redefines the industry standard for stainless steel surface treatment, but also reveals the inevitable path for the development of high-end manufacturing equipment-achieving exponential improvement in production efficiency through innovation in physical principles. When traditional technology encounters a technological ceiling, only by embracing innovation can we win the future in industrial transformation.