In many manufacturing and processing industries, deburring the workpiece surface is an important process link. Burrs not only affect the cosmetic quality of a product, but can also lead to poor functionality and performance. In order to efficiently deburr and improve the surface quality of workpieces, magnetic polishing machines have become a widely used solution. This article will discuss the application of magnetic polishing machines in deburring, as well as the advantages and tips for using them.
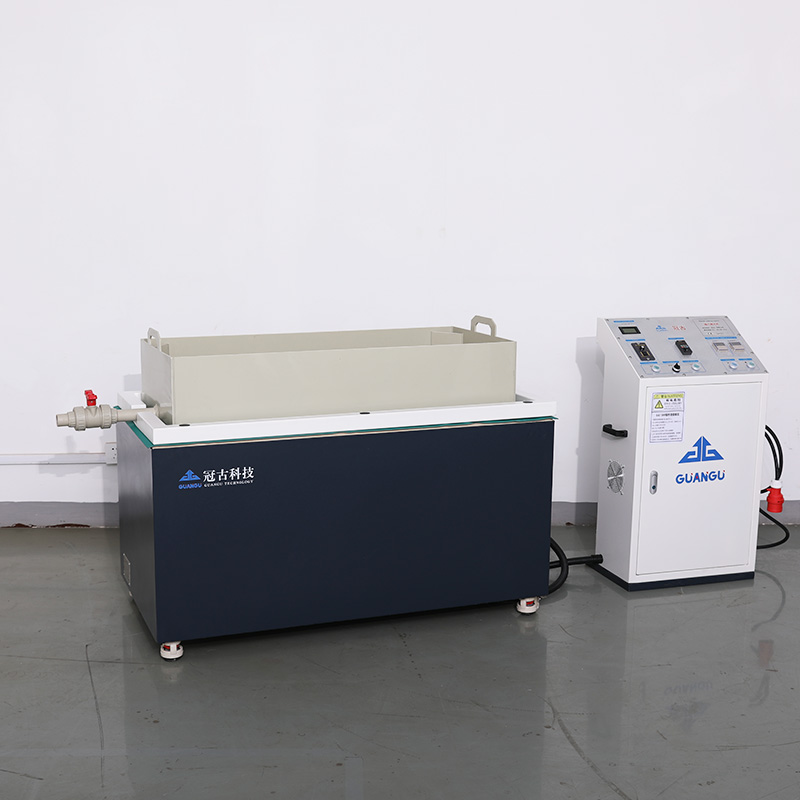
1. Application of magnetic polishing machine in deburring
The magnetic polishing machine can quickly and effectively remove the burr on the surface of the workpiece by using the action of magnetism and abrasives. Its application is mainly reflected in the following aspects:
Surface smoothing: The magnetic polishing machine rotates the workpiece and applies magnetic force to make the abrasive evenly distributed on the surface of the workpiece, thereby achieving surface smoothing. This eliminates or reduces burr formation and improves surface finish.
Corner rounding: During the machining process, the corners of the workpiece are often prone to burrs. By using appropriate abrasives and parameters, the magnetic polishing machine can effectively remove the burrs on the corners and achieve rounding, making the edges of the workpiece smoother and safer.
Micro-level polishing: The magnetic polishing machine can polish at the micro-level to remove tiny burrs and blemishes on the surface of the workpiece. This high-precision polishing can improve the surface quality of the workpiece and meet the applications that require high precision and smoothness.
Second, the advantages of magnetic polishing machine
Magnetic polishing machines have the following advantages in deburring:
Efficient and fast: The magnetic polishing machine adopts the method of automatic rotation and magnetic force, which can process multiple workpieces at the same time and improve production efficiency. The deburring process is fast and uniform, reducing the time and cost of manual operations.
Uniform and consistent: The magnetic polishing machine can evenly distribute the abrasive on the surface of the workpiece to achieve a uniform deburring effect. The problems of unevenness and quality fluctuation that may exist in manual operation are avoided.
Strong controllability: The magnetic polishing machine can achieve precise control of the deburring process by adjusting the magnetic force, abrasive type and process parameters, etc. According to the characteristics and requirements of different workpieces, the parameters can be adjusted to obtain the best deburring effect.
3. Use skills and precautions
There are a few tips and considerations to consider when using a magnetic polisher for deburring:
Select the appropriate abrasive: According to the workpiece material and deburring requirements, select the appropriate abrasive type and particle size. Different abrasives have different deburring effects and surface qualities.
Adjust process parameters: According to the size, shape and material characteristics of the workpiece, reasonably adjust the parameters such as the speed, magnetic strength and polishing time of the magnetic polishing machine to obtain the best deburring effect.
Regular maintenance and cleaning: Regularly clean the abrasive tank and liquid circulation system of the magnetic polishing machine to ensure its normal operation and stable polishing effect.
Safe operation: When using a magnetic polishing machine, pay attention to safe operation. Wear appropriate personal protective equipment to avoid the risk of abrasive splash and mechanical injury.
Magnetic polishing machines demonstrate the advantages of high efficiency, uniformity and controllability in deburring. Its applications cover surface planarization, corner rounding and micro-level polishing, providing reliable solutions for manufacturing and processing in various industries. When using a magnetic polishing machine for deburring, it is necessary to pay attention to selecting the appropriate abrasive, adjusting the process parameters, and ensuring safe operation and regular maintenance. Through the reasonable application of the technology and usage skills of the magnetic polishing machine, the quality and function of the workpiece surface can be effectively improved to meet the requirements of high-quality products.