Forging parts in China’s manufacturing industry occupies an important position, and the quality of its surface treatment directly affects the use of parts performance and life. This paper mainly introduces the application of magnetic polishing machine in the surface treatment of forging parts, analyzes the advantages of magnetic polishing technology and its positive effect on improving the surface quality of forging parts.
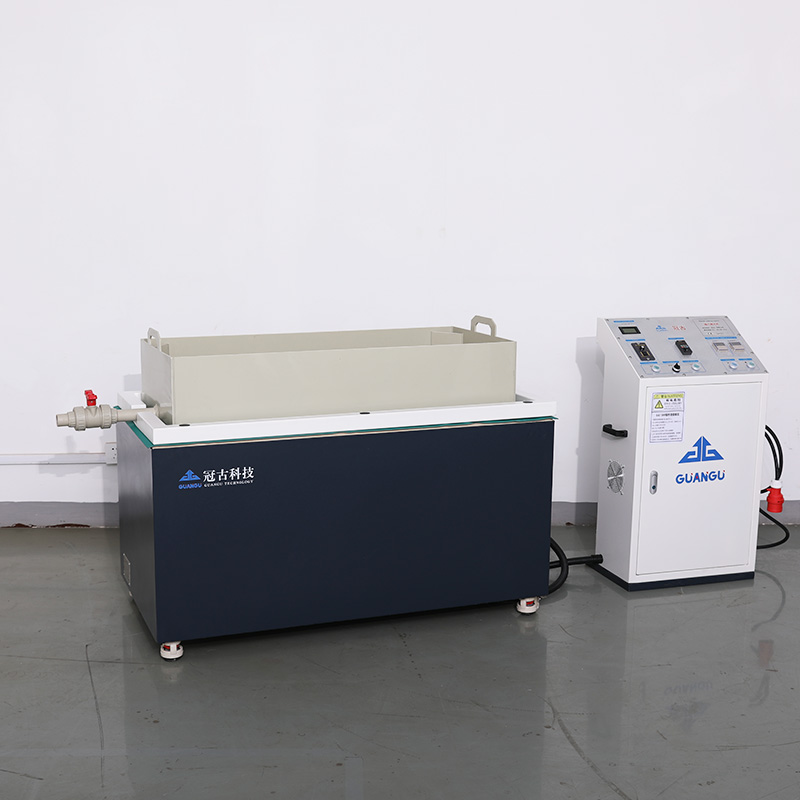
I. Introduction
With the rapid development of China’s manufacturing industry, forged parts are more and more widely used in aviation, aerospace, automotive, machinery and other fields. Forged parts in the manufacturing process, due to the influence of various factors, its surface often exists oxide skin, burrs, cracks and other defects. In order to improve the surface quality of forged parts, reduce the impact of defects on the use of performance, surface treatment technology is particularly important. Magnetic polishing machine as a new type of surface treatment equipment, gradually in the field of surface treatment of forging parts are widely used.
Second, the principle of magnetic polishing technology
Magnetic polishing machine using magnetic abrasive in the magnetic field, the role of the workpiece grinding, polishing. Its working principle is as follows: the workpiece is placed in the magnetic field, magnetic abrasive in the magnetic field force, adsorption on the surface of the workpiece. By adjusting the magnetic field strength and abrasive particle size, the abrasive material on the surface of the workpiece to carry out tiny cutting, extrusion, so as to achieve the purpose of removing the oxide skin, burr, reduce surface roughness.
Third, the application of magnetic polishing machine in the surface treatment of forging parts
1. Remove oxidized skin
Forging parts formed at high temperatures, the surface will produce a layer of oxide skin. This layer of oxidized skin will affect the dimensional accuracy of the parts, surface quality and subsequent processing. Magnetic polishing machine using magnetic abrasive cutting effect, can effectively remove the oxide skin, improve the surface quality of the parts.
2. Remove burrs
Forging parts in the molding process, the edge parts are prone to burrs. Magnetic polishing machine by adjusting the distribution of magnetic field, so that the abrasive on the burr parts to focus on grinding, to achieve the purpose of removing burrs.
3. Reduce surface roughness
Magnetic polishing machine adopts tiny magnetic abrasive, fine grinding on the surface of the workpiece, can effectively reduce the surface roughness, improve the use of parts performance.
4. Improve the surface stress state
Forged parts are subject to different degrees of stress during the manufacturing process. Magnetic polishing machine in the removal of surface defects at the same time, help to improve the surface stress state of the parts, improve their fatigue life.
Fourth, magnetic polishing technology advantages
1. High efficiency and energy saving
Magnetic polishing machine adopts magnetic abrasive, high grinding efficiency, low energy consumption, suitable for mass production.
2. Stable processing quality
Magnetic polishing machine processing process, the abrasive on the surface of the workpiece uniform force, stable processing quality.
3. Wide range of application
Magnetic polishing machine is suitable for forging parts of various shapes and sizes, with high versatility.
4. Environmental protection and no pollution
Magnetic polishing machine adopts water-based abrasive, no dust, noise pollution during processing, in line with the concept of green manufacturing.
V. Conclusion
Magnetic polishing machine in the surface treatment of forging parts has significant advantages, can effectively improve the surface quality of parts, reduce the impact of defects on the use of performance. With the continuous development of China’s manufacturing industry, magnetic polishing technology will play an increasingly important role in the field of surface treatment of forging parts.